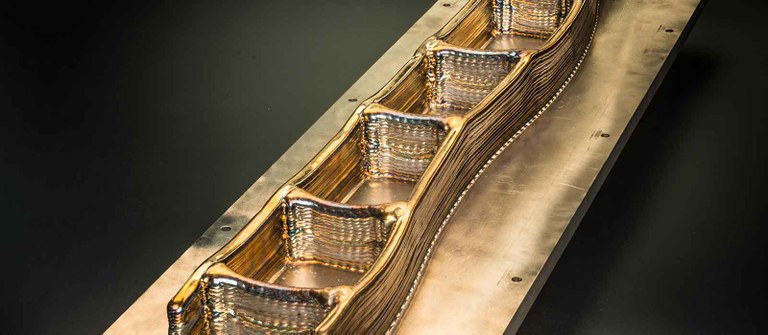
Applications and business drivers
APPLICATIONS
- Aerospace
- Oil and Gas
- Defence
- Architecture
- Product design
- Automotive
- Renewable energy
- Nuclear energy
- General engineering
BUSINESS DRIVERS and BENEFITS
Reduction in lead time
WAAM can enable reduction in lead times from years to weeks or even days.
Low capital cost
A six-axis robot (£50k), a power source and torch (£30k) and the clamping tooling (£10k) constitute the basic WAAM hardware, for a total of £90k. This system is suitable for deposition of steel and aluminium. In case of titanium, given the additional requirement for an inert atmosphere, an enclosure might be necessary (an extra £20k).
Open architecture
The end user can potentially combine any brand of power source and manipulator retaining total control over the hardware. This is managed by software, WAAMsoft, which controls the process and can be adapted to the specific equipment available in the manufacturing cell. Furthermore, the user retains the freedom to change any deposition parameter; the software suggests the deposition parameters on a feature basis, but the user can customise them if required.
Part size
Materials such as aluminium or steel do not have a stringent requirement for gas shielding; consequently, the maximum part size is determined uniquely by the reach capability of the manipulator. For materials that require shielding such as titanium, the size is limited by the inner envelope of the chamber or tent used to create the inert atmosphere.
High deposition rates
Deposition rates are sufficiently high to make the deposition of large scale parts achievable in reasonable times. With rates ranging from 1 kg/h to 4 kg/h for aluminium and steel respectively, most parts can be manufactured within one working day. Higher deposition rates can be achieved (e.g. 10 kg/h), but this then compromises the fidelity of the part. For instance, at 10 kg/h, the BTF ratio can be as high as 10 for the final deposited part, which is effectively a preform, thus requiring significant machining as well as the deposition of much more material, making the process less attractive from an economic point of view. Keeping the deposition rate at medium levels (e.g. 1 kg/h for titanium and aluminium, and 3 kg/h for steel) ensures that a BTF ratio of <1.5 is always achieved, maximising the cost saving.
Material cost and utilisation
Welding wire is a cheap form of feedstock. Steel is priced between £2 /kg and £15 /kg (depending upon wire diameter and alloy composition), aluminium between £6 /kg and £100 /kg (depending upon wire diameter and alloy composition) and Ti–6Al–4V between £100 /kg and £250 /kg (depending upon wire diameter and alloy composition). Furthermore, wire avoids many of the challenges associated with powders such as control of particle size or distribution, which affect process performance. Finally, at the point of deposition, the wire is entirely molten and becomes part of the final structure, and the likelihood of contamination is low compared with powder.
Cost savings
WAAM can enable cost savings up to 70% when compared to machining from solid billet, or open-die forging.
Please note all costs for WAAM parts do include finish machining, even if the pictures show parts in the as-deposited conditions.
BAE Systems spar
Design option |
Mass (kg) |
BTF |
Cost (£k) |
Cost red. |
Original, machined |
17 |
6.5 |
7.2 |
- |
Original, WAAM |
17 |
2.2 |
5.1 |
29% |
Bombardier outboard landing gear rib (titanium)
Design option |
Mass (kg) |
BTF |
Cost (£k) |
Cost red. |
Original, machined |
20 |
12 |
16.2 |
- |
Original, WAAM |
20 |
2.3 |
5 |
69% |
Bombardier outboard landing gear rib (steel)
Design option |
Mass (kg) |
BTF |
Cost (£k) |
Cost red. |
Original, machined |
36 |
12 |
1.6 |
- |
Original, WAAM |
36 |
2.3 |
0.7 |
55% |
An engine pylon mount
Design option |
Mass (kg) |
BTF |
Cost (£k) |
Cost red. |
Original, machined |
7.6 |
5.1 |
2.5 |
- |
Original, WAAM |
7.6 |
1.5 |
2.4 |
4% |
Topologically optimised, machined |
3.9 |
6 |
1.5 |
39% |
Topologically optimised, WAAM |
3.9 |
1.5 |
1.1 |
55% |
An aluminium wing rib
Design option |
BTF |
Cost (£k) |
Cost red. |
Machined from solid |
45 |
4.9 |
- |
WAAM option 1 |
2.9 |
1.7 |
65% |
WAAM option 2 |
12.3 |
2 |
58% |
Titanium wing frame
Design option |
BTF |
Cost (£k) |
Cost red. |
Machined from solid |
69 |
4.9 |
- |
WAAM option 1 (thin substrate) |
7 |
2.6 |
67% |
WAAM option 2 (thick substrate) |
8 |
2.4 |
69% |
Example 1 of a titanium structural part (including comparison with another high deposition rates process)
WAAM |
HiDR process |
Saving by using WAAM |
|
Deposition BTF |
3 |
10 |
- |
Substrate BTF |
12 |
12 |
- |
Overall BTF ratio |
8 |
11 |
- |
Cost of part machined from solid |
£ 12155 (BTF = 60) |
- |
|
Cost of AM part |
£ 3189 |
£ 4389 |
27% |
Finished product mass |
3 kg |
3 kg |
- |
Deposited mass |
4 kg |
13 kg |
69% |
Cost reduction |
74% |
64% |
- |
Example 2 of a titanium structural part (including comparison with another high deposition rates process)
WAAM |
HiDR process |
Saving by using WAAM |
|
Deposition BTF |
2 |
10 |
- |
Substrate BTF |
3 |
3 |
- |
Overall BTF ratio |
3 |
5 |
- |
Cost of part machined from solid |
£ 16184 (BTF = 30) |
- |
|
Cost of AM part |
£ 3258 |
£ 6179 |
48% |
Finished product mass |
8 kg |
8 kg |
- |
Deposited mass |
5 kg |
32 kg |
84% |
Cost reduction |
80% |
62% |
- |