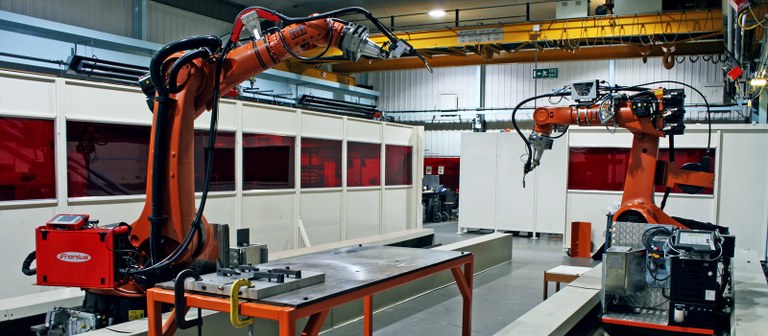
Flexible manufacturing
Reconfigurable, open-architecture hardware to match the requirements of your company.
Thanks to the support of Global Robots, Cranfield can count on a unique facility based on:
- two 10-metre long robot tracks
- two KUKA robots equipped with automatic tool changers
- two welding power source
- a fully-interfaced programmable logic controller
The cell will be soon completed with the addition of two servo positioners. The two robots can reach a total distance of 12 metre, meaning parts up to this size in aluminium and steel can be built on this system. With the implementation of our local shielding device, soon it will be possible to deposit parts in titanium also of this size.
The capability of switching instantaneously from one process to another results in the possibility of performing the following operations, in-process:
- additive
- subtractive
- inspection
- monitoring
- metrology
Additive to deposit material; monitoring, to ensure no undesirable changes are occurring in the deposition parameters; metrology, to check whether any deviation from the desired shape is happening; inspection, to make sure no defects exist; and machining, to finish the part or to eliminate the defective layer prior to resuming the additive operations.
In this way, we can achieve
- fully finished parts, in a single setup
- fully quality-assured parts through inspection of every layer, thus potentially reducing the scrap rate to zero.