Study of fundamental laser material interaction parameters in powder melting
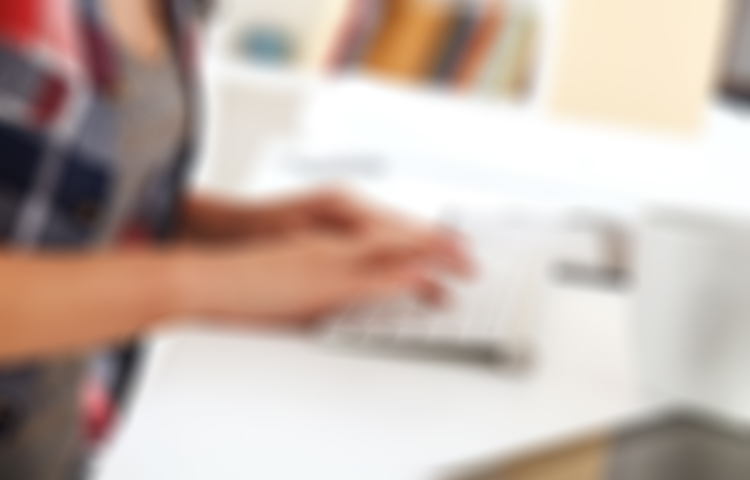
Processing parameters in the majority of powder bed-based additive manufacturing are developed using the system parameters of a particular machine. In such a case the process is optimised only for this particular machine with a particular optical set-up, which imposes transferability issues when applying the process on different machines. In this project powder build characteristics is investigated from the perspective of spatial and temporal energy distribution. A set of laser material interaction parameters, which characterise the footprint of laser energy on the surface of workpiece is used to control the bead profile of powder deposits. These parameters define the process uniquely and are laser system-independent.
The overall goal of this project is to make the selective laser melting process more robust and transferable between different powder bed systems.
In order to have a robust powder bed laser additive manufacturing the interaction between laser and powder and its effect on the fusion characteristics need to be understood. Since built parts consist of many individual tracks fused together according to the specified tool path, the quality of the whole part is strongly determined by the stability of the melpool of each track. In this project powder bed is treated as a welding problem, where the stability of individual tracks is investigated. The main focus is put on parameters controlling the profile of fused tracks and process stability.
In the initial stage of the project solid steel with homogenous and well known properties is used to study the effect of laser energy on the bead profile and transition between processing regimes for a wide range of beam diameters. Then the fusion characteristics between powder and solid material with the same bulk properties are compared. An open architecture powder bed set-up is used to enable us to use a range of laser sources with different optical set-ups. Bead-on-plate welds and powder track are performed with a wide range of beam diameters ranging from 6 mm to 30 µm to understand the process from macro and mezzo scale to real conditions used in commercial powder bed machines. The work is supported by mezzo scale modelling of melt the pool.