Laser smoothing of WAAM surfaces
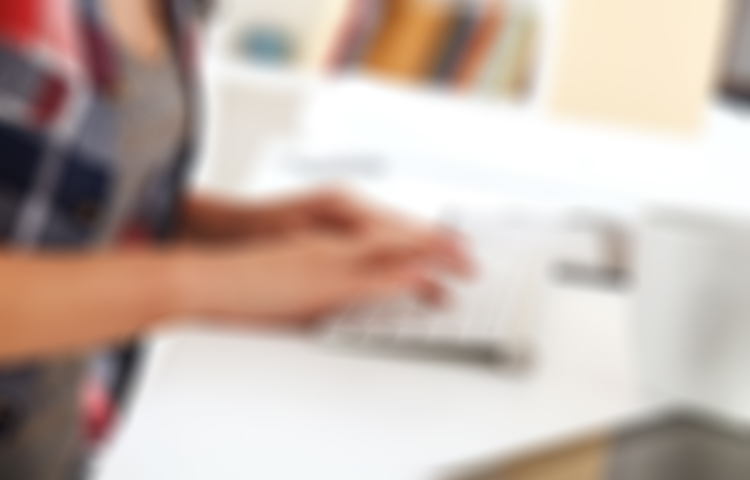
As a result of deposition of many welding beads the WAAM parts exhibit periodic surface waviness, the depth of which increases with increasing layer thickness and deposition rate. Although in most cases such surface has good structural integrity and is fully functional, but in some applications it is desirable to machine certain surfaces of the component. However the cost of machining of the complex parts in titanium in particular is significantly high. In this project a laser finishing, as an alternative method to mechanical machining, is investigated. A laser source is used to remelt the surface of WAAM parts and smoothen it by the controlled melt flow.
Project description:
Laser polishing, similarly as other laser processes, relies on a balance between the applied laser energy and heat flux in the material. The melting behaviour in conduction welding is highly dependent on the thermal properties of the material and absorptivity, which is affected by the surface roughness. In addition the laser energy, its spatial and temporal distribution along with the wavelength also play a crucial role. In laser processing the total energy and its spatial distribution can be changed independently, which on one side enables the user to tailor the processing conditions, but on the other hand this makes process more difficult to control. There are many ways of applying the laser energy to the surface using different spot sizes of laser beam, different intensity distribution and temporal modes, i.e. pulsed, continuous.
In this project the effect of intensity distribution and shape of the beam on the profile of shallow penetration conduction welds are investigated. Different optical set-ups and novel tailored optical components to achieve different beam projections with different spot sizes will be used. A relationship between the surface roughness and the remelting depth necessary for efficient smoothing is investigated. It is envisaged that for a given material the process conditions i.e. size and depth of fusion zone is controlled by the fundamental interaction parameters of spatial energy distribution, such as power density and energy. Also benefits of pulsed lasers will be investigated. The least invasive conditions in terms of heat effects and residual stresses will be sought.